1. Hydraulic Design: Balancing Flow Capacity and Sediment Control
The peak flow rate (Q = A × V) remains the cornerstone of culvert sizing. Manning’s equation (n=0.024 for corrugated steel) is critical for calculating cross-sectional dimensions, as demonstrated in Queensland’s 2018 flood project, where 3 m × 2 m culverts successfully managed 25 m³/s flows. Undersizing risks overtopping, while oversizing exacerbates sediment deposition—a trade-off requiring precise hydraulic modeling.
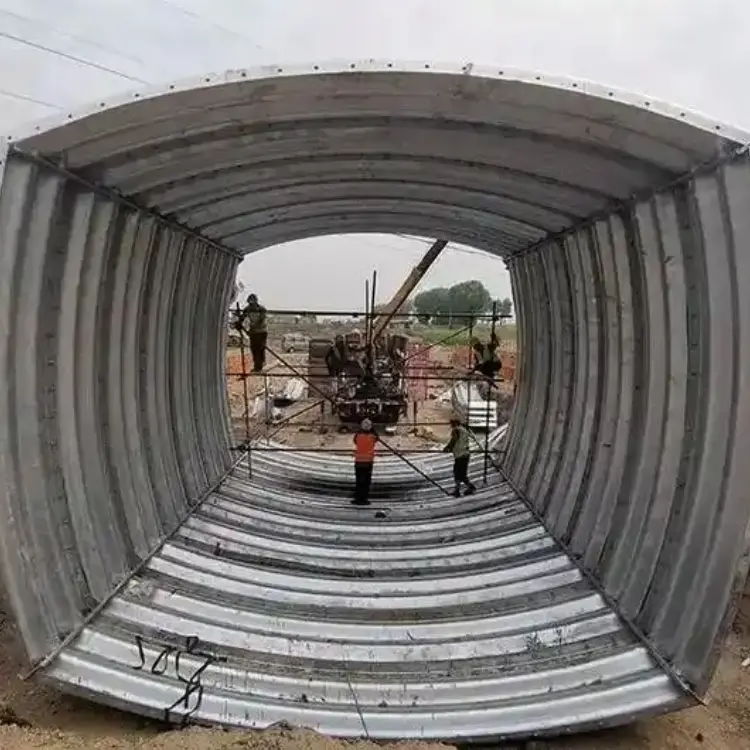
2. Material Selection: Corrosion and Abrasion Resistance
- Galvanization: A 275 g/m² zinc coating (ASTM A123) ensures 50+ years of service in saline environments, validated by Florida’s coastal drainage systems.
- Panel Thickness: Debris-laden flows demand ≥3 mm steel; Nepal’s 2021 monsoon failures highlighted the inadequacy of 2 mm panels under similar conditions.
3. Structural Adaptations for High-Velocity Flows
For velocities exceeding 3 m/s, trapezoidal rib reinforcements (e.g., Netherlands’ Room for the River project) reduce scour damage by 60%. Bolted joints and internal baffles further enhance stability in turbulent flows.
4. Installation Best Practices
- Foundation Preparation: A 150–300 mm compacted granular base with geotextile (per Alberta’s 2023 case) minimizes settling by 12%.
- Leak Prevention: Butyl rubber gaskets (ASTM D2000), as used in Vietnam’s Mekong Delta, eliminate joint leakage.
5. Environmental and Regulatory Compliance
NSF-61 certification is non-negotiable for potable water zones. Chile’s 2020 project retrofit costs underscored the risks of non-compliant materials exceeding EPA zinc limits.
Case Study: Modular Steel Culverts in Post-Hurricane Recovery
Texas’ Brazos River replacement project (2017–2023) showcased the advantages of 4 m × 2.5 m galvanized steel culverts:
- 40% faster bolt-together installation versus cast-in-place concrete.
- Zero deformation post-2023 floods (LiDAR-verified).