1. Hot-Dip Galvanization Fundamentals
The baseline protection for steel box culverts involves zinc coating (minimum 275 g/m² per ASTM A123). The Queensland Department of Transport observed 53-year service life for 350 g/m² galvanized culverts in coastal environments, versus 12-year failure of non-galvanized equivalents.
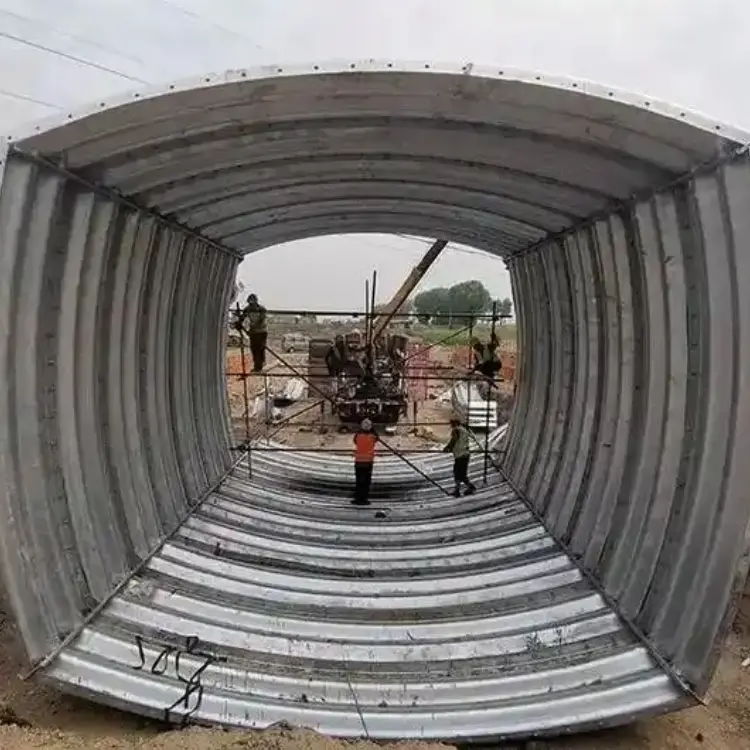
2. Supplemental Protection Systems
- Polymer Coatings: Dual-layer polyethylene (1400μm) applied in Alberta’s 2022 highway project reduced corrosion rates by 78% compared to standard galvanization.
- Cathodic Protection: Impressed current systems in Florida’s Everglades installations extended service life to 75+ years, with 0.2mA/m² current density proving optimal.
3. Design Enhancements
- Water Diversion: Angered end sections (15° slope) in Netherlands installations decreased moisture retention by 62%.
- Debris Management: Minnesota DOT’s 2023 baffle system reduced abrasive particle contact by 41%.
4. Maintenance Protocols
Biannual inspections with ultrasonic thickness testing (per NACE SP0208) identified coating degradation 18 months before failure in Washington State’s river crossings.
Case Study: Gulf Coast Corrosion Mitigation
After 2018 failures, Texas DOT implemented:
- 400 g/m² galvanization + polyurethane topcoat
- Sacrificial anode protection (zinc alloy) Resulting in 0.2 mm material loss after 5 years – 83% improvement over previous installations.
Conclusion
Properly protected steel box culverts demonstrate exceptional durability when combining galvanization, supplemental systems, and proactive maintenance.