Failure Modes and Solutions for Prestressed Corrugated Pipes: Comprehensive Analysis and Enhancements
1. Material-Specific Corrosion Mechanisms and Advanced Solutions
Metal Pipes Corrosion
- Primary Failure Mode: Chloride-induced pitting corrosion remains prevalent, particularly in coastal environments where studies show galvanized steel pipes can lose 0.8mm/yr thickness in splash zones
- Enhanced Protection Methods:
- Multi-layer zinc-aluminum coatings (Galfan®) with 85μm thickness
- Optimized cathodic protection systems operating at -1.1V potential (NACE SP0169 compliant)
- Corrosion-resistant cast iron formulations with improved microstructure
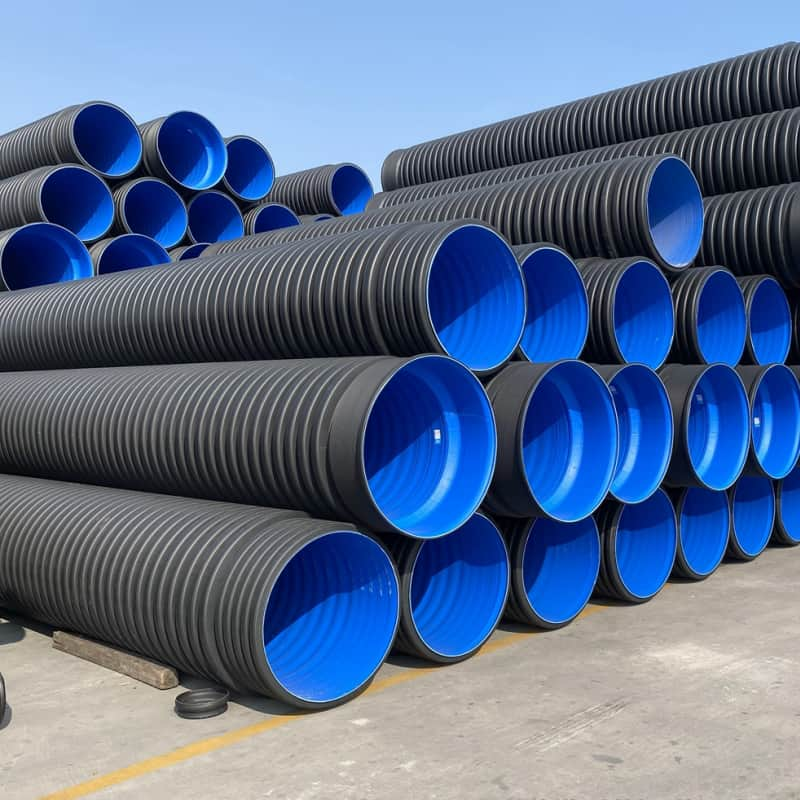
Plastic Pipes Degradation
- Critical Issues: HDPE pipes exhibit stress cracking when exposed to hydrocarbons, with documented cases in refinery environments
- Material Improvements:
- PE100-RC grade materials with controlled crystallinity (≤15%)
- Protective composite sleeves for contamination-prone areas
- Finite element modeling to predict failure modes in UPVC branch pipes
2. Prestress Loss Mechanisms and Mitigation Strategies
Steel Pipe Systems
- Documented Problems: Improper grouting has caused up to 12% prestress loss in spiral-rib pipes
- Technical Solutions:
- Advanced ultrasonic testing (ASTM E797) for post-tensioning verification
- Electrochemical chloride extraction for corroded tendons
- Numerical modeling of joint responses under ground subsidence
Plastic Pipe Systems
- Creep Challenges: Documented cases show 9mm deflection from creep-induced relaxation
- Design Improvements:
- 0.6× yield strength safety factor implementation
- Scheduled re-tensioning protocols (5-year intervals)
- Optimized bulge forming processes for UPVC pipes
3. Joint Integrity Solutions for Extreme Conditions
Metal Pipe Joints
- Thermal Movement Issues: ΔT=80°C environments cause bolt shear failures
- Engineering Solutions:
- Slotted connection systems allowing ±50mm movement
- Neoprene gaskets with Shore A 70 hardness
- Tire-derived aggregate (TDA) mitigation measures for jointed pipes
Plastic Pipe Joints
- Installation Failures: Soil settlement causes electrofusion joint leaks
- Improved Techniques:
- Precision laser-aligned coupling systems
- Engineered sand bedding with 95% compaction
- Numerical analysis of joint failure modes under subsidence
4. Flow-Related Deterioration and Hybrid Protection
High-Velocity Applications (>3m/s)
- Metal Pipe Solutions:
- Centrifugally cast cement linings
- Computational fluid dynamics optimized designs
- Plastic Pipe Solutions:
- Ultra-high MW polyethylene liners
- FEM-simulated branch pipe formations
Case Study Validation
- Documented Success: Hybrid lining systems reduced wear by 92% in high-flow environments
Enhanced Preventive Maintenance Framework
Metal Pipe Inspection
- Annual MFL inspections per API 116
- Advanced numerical modeling of failure modes
Plastic Pipe Monitoring
- Biannual strain gauge measurements (ISO 527-1)
- FEM simulation-based condition assessment
Cross-Material Best Practices
- Implementation of TDA-based mitigation measures
- Regular review of computational modeling results
- Scheduled verification of cathodic protection systems