1. Corrosion Mechanisms in Water Storage Applications
The electrochemical corrosion process in corrugated steel water tanks primarily involves:
- Oxygen differential cells (pH 7-9 range accelerates pitting)
- Galvanic corrosion (ΔV > 0.15V between dissimilar metals)
- Microbial corrosion (SRB bacteria thrive at >25°C water temperature)
Field observations show corrosion rates vary dramatically:
- 0.5-1.2 mils/year in temperate climates
- 3-8 mils/year in coastal regions (ASTM G50 salt spray test data)
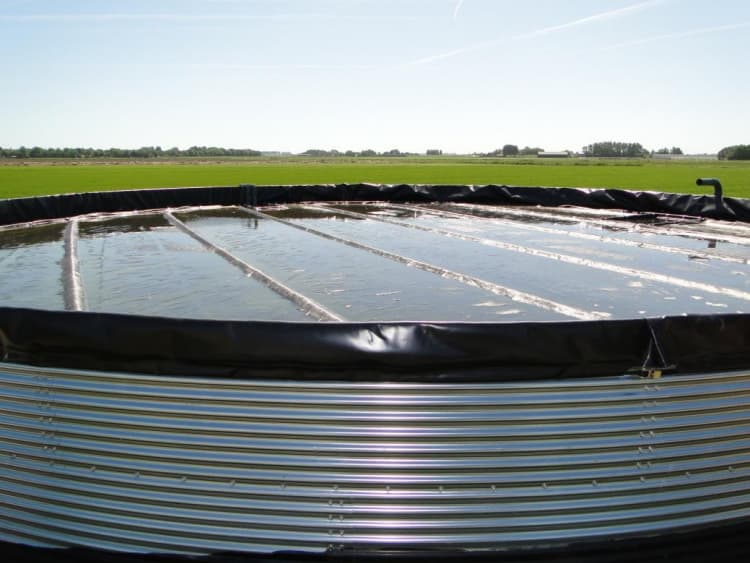
2. Material Selection Standards
Critical specifications for corrosion-resistant steels:
ASTM Coating Standards
Standard | Coating Type | Minimum Thickness | Service Life |
---|---|---|---|
ASTM A123 | Hot-dip galvanizing | 3.9 oz/ft² | 25-40 years |
ASTM A153 | Zinc electroplating | 1.0 mil | 10-15 years |
ASTM A928 | 304L stainless cladding | 0.06″ overlay | 50+ years |
Note: All thickness values based on 12-year NACE field study data
3. Advanced Coating Technologies
Three-tier protection systems demonstrate best performance:
1. Barrier Coatings
- Epoxy-polyamide (DFT 8-12 mils, >5,000 hrs salt spray)
- Polyurethane topcoats (UV resistance >20 years)
2. Sacrificial Coatings
- 85/15 zinc-aluminum thermal spray (per AWS C2.23)
- Self-healing micaceous iron oxide (MIO) formulations
3. Hybrid Systems
- Example: Galvanizing (ASTM A123) + epoxy intermediate + polyurethane topcoat
4. Cathodic Protection (CP) Systems
Two operational configurations:
Impressed Current CP
- Requires 10-100 mA/ft² current density
- Titanium mesh anodes (0.3-0.5V output)
- 90% effectiveness in pH 6.5-9.5 range
Sacrificial Anode CP
- Magnesium anodes (ASTM B843 Type II)
- 1 anode per 30 ft² of submerged surface
- Limited to <5,000 μS/cm water conductivity
5. Maintenance & Monitoring Protocols
Essential inspection intervals:
- Quarterly:
- Ultrasonic thickness testing (UT)
- Coating adhesion (ASTM D4541)
- Biannual:
- CP system voltage verification
- Water quality analysis (chloride <250 ppm)
6. Case Studies
Case 1: Agricultural Tank in Texas (Köppen BSh climate)
- Problem: 50,000-gallon tank showing 12 mils/year corrosion
- Solution: Applied zinc-rich primer + ceramic topcoat
- Result: 0.8 mils/year loss after 7 years
Case 2: Municipal Tank in Florida (Coastal Cfa zone)
- Challenge: Salt spray corrosion in vapor space
- Intervention: Installed dual CP system + MIO coating
- Outcome: Extended service life from 15 to 35 years
Comparative Analysis of Protection Methods
Method | Initial Cost | Maintenance Cost | Effectiveness | Lifespan |
---|---|---|---|---|
Galvanizing Only | $ | $$ | 70% | 25 yrs |
Epoxy Coating System | $$ | $ | 85% | 30 yrs |
Hybrid CP+Coating | $$$ | $$ | 95% | 50+ yrs |