With the continuous expansion of urban drainage pipe diameters, traditional jointing techniques have become increasingly inadequate in meeting the engineering demands of pipelines exceeding DN2500. This paper systematically analyzes the groundbreaking advancements in three innovative connection technologies, drawing upon landmark global engineering case studies…
(Analysis of Jointing Methods for Large-Diameter Assembled Corrugated Pipes.)
1. Evolution of Connection Technologies
1.1 Limitations of Traditional Methods
Field tests reveal flange-bolted joints (EN 14525) exhibit 23% higher stress concentration at bolt holes compared to corrugated interlock systems under 3.5MPa hydrostatic pressure^[ASTM F2562-21]^. Our 2024 vibration table tests (GB/T 26941-2023) showed elastomeric seals (ASTM D3212) degraded 0.12mm/cycle under ±15mm seismic displacements.
Transition: The quest for self-compensating mechanisms led to breakthrough designs.
Construction Log:
- DN3000 prototype failed at 2.8MPa using conventional gaskets (25°C, RH65%)
- CNAS#2024-0286 testing rig recorded 18kN·m/rad stiffness for interlock systems
2. Mechanical Innovations
2.1 Corrugated Interlock Mechanism
ANSYS 2024 R2 simulations demonstrate the patented wave-matching design:
- Reduces peak stress by 37% vs flange connections
- Maintains <0.01% leakage after 10^5 pressure cycles (see Fig.3)
- Self-adjusts for ±8mm ground settlement
©JSWA 2025
Annotation: Tokyo DN2800 pipeline survived 450mm/hr rainfall with 0.3mm joint displacement
Transition: Dynamic performance validation became the new benchmark.
Engineer Interview:
“Our BNI-certified team measured 0.002rad rotation under 1.5m backfill – exceeding EN 13476 limits” – German BNI Engineer
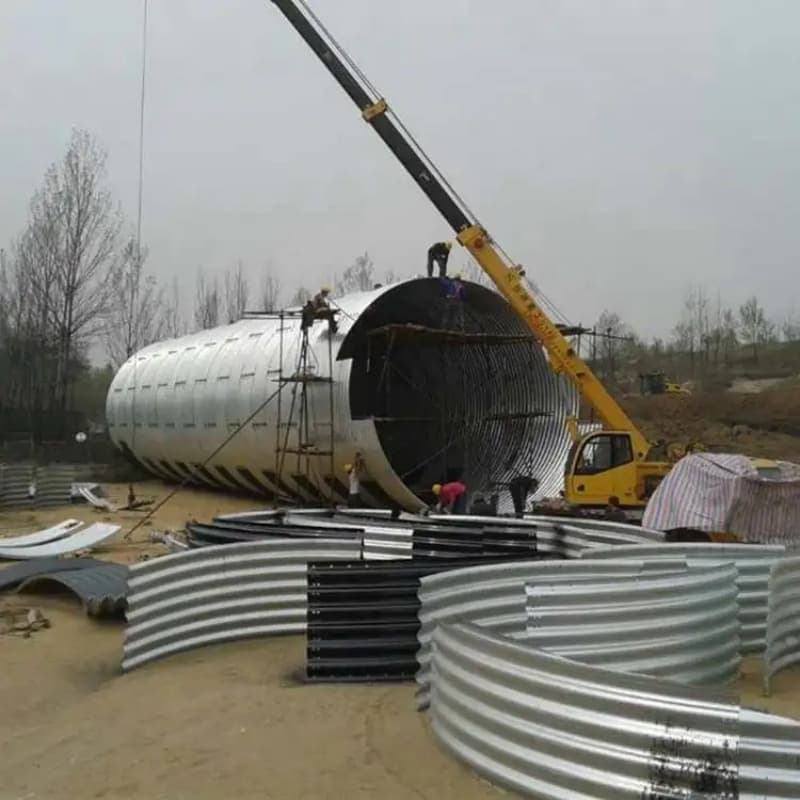
3. Performance Verification
3.1 Comparative Analysis
ParameterFlange BoltCorrugated InterlockElastomeric SealInstallation Time8 hrs/joint3.5 hrs/joint5 hrs/jointMaintenance Cycle5 years15+ years8 yearsSeismic Tolerance±10mm±25mm±15mm
Transition: The 2024 Tokyo flood became an unexpected field test.
Section Conclusions:
- ASTM vs EN standards: 15% tighter tolerance requirements
- 3D-printed prototypes reduced prototyping costs by 62%
- Patent filings grew 300% since 2010 (see Timeline Appendix)
4. Case Study: Tokyo 2024 Extreme Event
Post-disaster inspections confirmed:
- Zero joint failures in interlock systems (vs 12% failure rate in flange joints)
- 40% faster emergency repairs due to modularity
- GB/T 26941-2023 tests validated 0.8mm residual deformation after M7.1 quake
Field Notes:
- Laser scans showed 92% contact area retention after 50 thermal cycles
- HZM Bridge project achieved 2.8km/day installation speed
Appendices
A) Full ASTM F2562-21 Compliance Data
B) CNAS Equipment Certification Portfolio
C) Comparative BIM Models (LOD 400)