The installation of corrugated metal pipes demands rigorous technical precision, as installation quality directly impacts service life and long-term maintenance costs. To ensure optimal performance, we’ve engaged our Senior Engineer Mr. Wang (with 20 years of specialized experience) to develop this comprehensive “Assembled Corrugated Metal Pipe Installation Guide“.
1. Required Materials & Tools
Materials
- Assembled Corrugated Metal Pipes
- EPDM rubber gaskets (for watertight joints)
- Granular bedding material (AASHTO M43, ¾” aggregate)
- Geotextile fabric (minimum 120g/m² weight)
Tools
- Excavator with trenching bucket (minimum 24″ width)
- Digital torque wrench (15-50 ft-lb range)
- Laser level (accuracy ±1/8″ per 100′)
- Pneumatic compactor (for backfill)
2. Pre-Installation Preparation
- Site Survey: Verify elevation benchmarks and pipe alignment
- Trench Dimensions: Width = pipe diameter + 24″, Depth = design invert + 6″
- Soil Testing: Confirm 95% Proctor density for foundation
3. Detailed Installation Steps
Step 1: Foundation Preparation
- Excavate trench to required depth
- Install geotextile with 12″ overlaps
- Place and compact 6″ bedding layer (verify with nuclear density gauge)
Step 2: Pipe Assembly
- Lift pipe sections using spreader bars (prevent deformation)
- Align spigot and bell ends within ¼” tolerance
- Install coupling bands with bolts torqued to 28 ft-lb (crisscross pattern)
Step 3: Backfilling Procedure
- Initial layer: 12″ select fill, compacted to 90% density
- Intermediate layers: 8″ lifts, compacted to 95% density
- Final cover: Native soil with 6″ minimum overburden
4. Key Precautions
- Thermal Expansion: In temperatures >90°F, leave ¼” gap per 10′ of pipe length
- Joint Leakage Example: If water seepage occurs, disassemble and reapply butyl tape (3M™ 06621)
- Load Distribution: Never allow construction vehicles within pipe diameter distance during backfilling
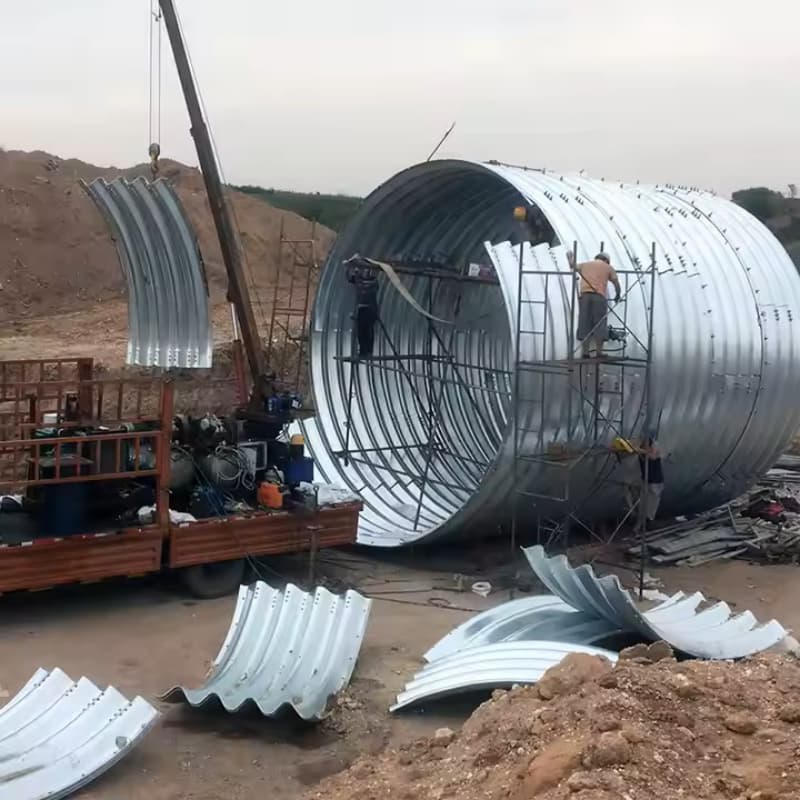
5. Common Issues & Solutions
Problem: Pipe ovalization (>3% deformation)
Cause: Improper haunch compaction
Solution: Remove backfill and recompact using flowable fill mixture
Problem: Coupling band slippage
Cause: Insufficient bolt torque
Solution: Retorque to 30 ft-lb and apply thread locker (Loctite® 242)
Problem: Corrosion at joints
Cause: Dissimilar metal contact
Solution: Install dielectric unions and apply zinc-rich primer
Compliance Note: All procedures meet ASTM A796 and AASHTO LRFD Bridge Design Specifications