Revolutionizing Infrastructure: The Assembled Corrugated Pipes Advantage
Defining Modular Pipe Systems
Imagine construction sites where pipe installation happens at triple speed. Assembled corrugated pipes (modular corrugated conduits) make this possible through their unique bolted-segment design. Unlike monolithic pipes, these corrugated steel assemblies combine:
Prefabricated galvanized steel panels (SS400/Q235 grade, ≥63µm zinc coating)
Precision-engineered wave patterns enhancing structural integrity
On-site bolt-together assembly reducing downtime
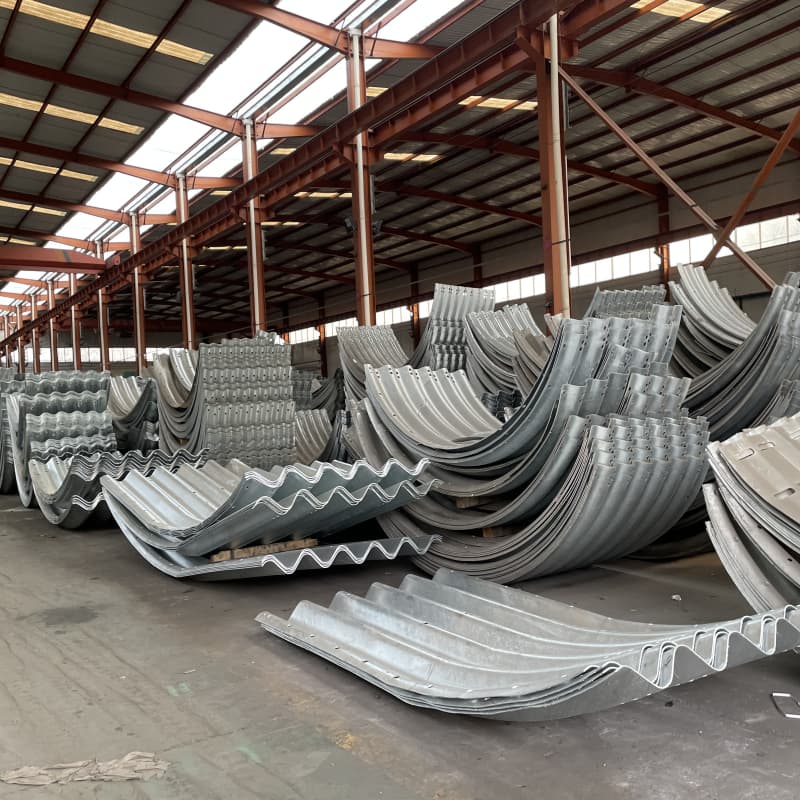
Structural Marvels in Metal
Material Science Breakthroughs
Galvanized steel dominates, but polymer composites now challenge traditional materials in corrosive environments. The secret? A 63µm zinc armor that outlasts conventional coatings.
Engineering the Waveform
That distinctive corrugation isn’t just aesthetic. Each ripple:
Absorbs 3-5mm ground movement
Distributes radial loads 40% more efficiently
Maintains flexibility under seismic stress
Where Innovation Meets Infrastructure
Transportation Networks Transformed
Highway culverts using these bolted corrugated systems report:
72% faster installation than concrete
50-year lifespans with minimal maintenance
Urban Stormwater Solutions
Municipalities are replacing aging systems with modular corrugated drainage that handles:
300% greater flow capacity
-60°C to +80°C temperature extremes
Saltwater corrosion resistance
Performance Beyond Expectations
The Installation Revolution
Three crews can install 100m of 2m-diameter pipe in one shift. Traditional methods require five days for equivalent work.
Cost Calculator
Initial savings: 25-30% vs. concrete
Lifetime savings: 40% when factoring in maintenance
ROI improvement: 18 months typical payback period
Stress Test Results
Field data shows these systems withstand:
0.3MPa internal pressure (equivalent to 30m water column)
200mm differential settlement
Seismic events up to 7.5 Richter