Introduction
Corrugated metal arch pipes serve as the resilient “vascular system” of modern cities, efficiently managing stormwater and wastewater drainage. However, prolonged exposure to harsh environmental conditions leads to corrosion, threatening their structural integrity. This article explores effective corrosion prevention methods and cost-efficient maintenance strategies, supported by real-world case studies.
1. Corrosion Prevention Techniques
1.1 Material Upgrades
Stainless steel offers superior corrosion resistance compared to conventional carbon steel. Its chromium-rich passive layer prevents oxidation, significantly extending service life in aggressive environments13.
1.2 Surface Treatments
- Galvanization: Hot-dip galvanizing (G90/G210 coatings) provides 25–50 years of protection by forming a zinc barrier3.
- Polymer Coatings: Epoxy, polyurethane, and fluorocarbon coatings isolate metal surfaces from moisture and chemicals5.
1.3 Protective Linings
- Cement Mortar Linings: Neutralize acidic water and prevent microbial corrosion (used in 60% of North American drainage projects)38.
- HDPE Liners: Flexible and abrasion-resistant, ideal for high-flow systems4.
1.4 Installation Best Practices
- Avoid surface scratches during handling.
- Ensure proper bedding and backfill to prevent electrochemical corrosion6.
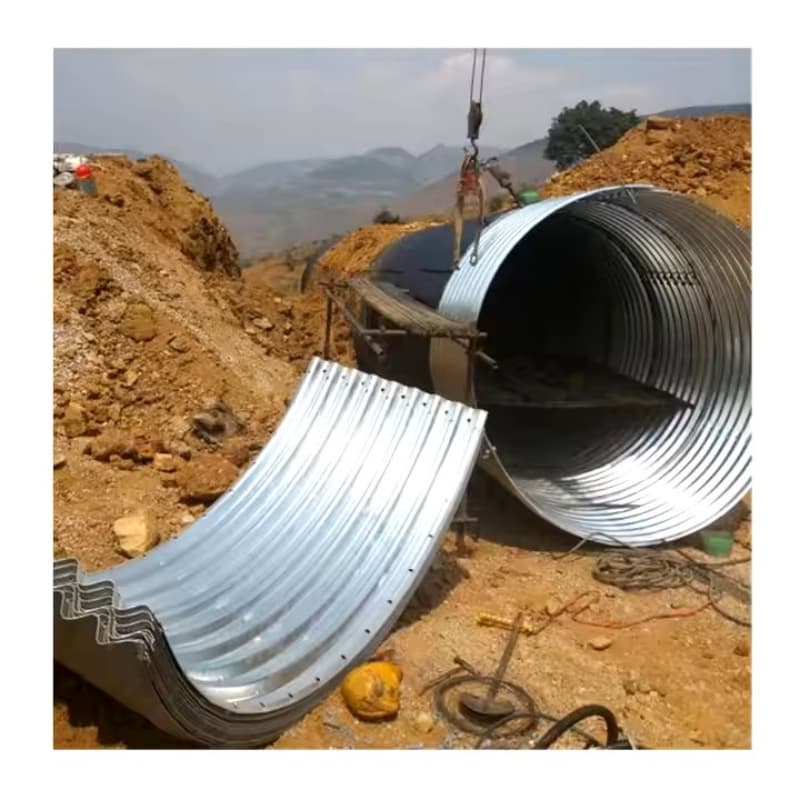
2. Cost-Effective Maintenance Strategies
2.1 Material Selection
- Lifecycle Cost Analysis: Stainless steel may have higher upfront costs but reduces replacement frequency by 40%1.
2.2 Adaptive Corrosion Protection
- Low-Risk Areas: Use economical coatings (e.g., bituminous paint).
- High-Risk Areas: Combine galvanization with cathodic protection3.
2.3 Proactive Maintenance
- Biannual Inspections: Identify early-stage pitting or coating damage.
- Sediment Removal: Prevents microbial-induced corrosion (MIC)6.
2.4 Smart Monitoring
- IoT Sensors: Detect pH, chloride levels, and wall thickness in real-time (e.g., Singapore’s PUB drainage network)5.
3. Case Studies
Case 1: Coastal Resilience in Miami, USA
- Challenge: Saltwater intrusion accelerated corrosion in drainage culverts.
- Solution: Aluminized Type 2 coatings + impressed current cathodic protection.
- Outcome: Service life extended from 20 to 50 years; maintenance costs reduced by 35%35.
Case 2: Industrial Zone in Rotterdam, Netherlands
- Challenge: Acidic runoff (pH 3.5) degraded conventional pipes.
- Solution: HDPE-lined corrugated pipes with sacrificial anodes.
- Outcome: Zero leaks reported over 15 years48.
Case 3: Mountain Tunnel Drainage, Switzerland
- Challenge: Freeze-thaw cycles and de-icing salts caused rapid corrosion.
- Solution: Epoxy-coated pipes with heated trace lines.
- Outcome: Eliminated winter failures; ROI achieved in 8 years16.
Conclusion
A holistic approach—combining advanced materials, tailored coatings, and predictive maintenance—can extend the lifespan of corrugated metal arch pipes beyond 75 years while optimizing lifecycle costs. Cities must prioritize corrosion management to safeguard critical drainage infrastructure35.