Industrial Applications
Corrugated Steel Storage Tanks provide optimal solutions for:
- Bulk water storage (potable/firefighting)
- Agricultural liquid fertilizers (NH3-proof coatings)
- Petroleum derivatives storage (API 650 Appendix J compliant)
- Wastewater buffer tanks (corrosion-resistant linings)
Engineering Advantages
Structural Design
- Galvanized steel panels (G550 AZ150, ASTM A653)
- 360° continuous corrugation for 35% greater hoop strength
- Bolted connections with EPDM gaskets (leak-tested @ 1.5x MAWP)
Key Advantages of Corrugated Steel Storage Tanks
1. Unmatched Structural Integrity
- 360° Corrugated Design: 35% greater hoop strength vs. flat panels (EN 1993-4-2)
- Seismic Resilience: Zone 4 certification (IBC 2018) with anti-buckling reinforcements
- Material Durability: 1.2-4.0mm hot-dip galvanized steel (G550 AZ150, ASTM A653)
2. Rapid Deployment & Cost Efficiency
- Modular Installation: 40% faster assembly than welded tanks (typical 5,000m³ tank: ≤8 weeks)
- Minimal Site Prep: No heavy foundation requirements (suitable for 30kPa soil bearing capacity)
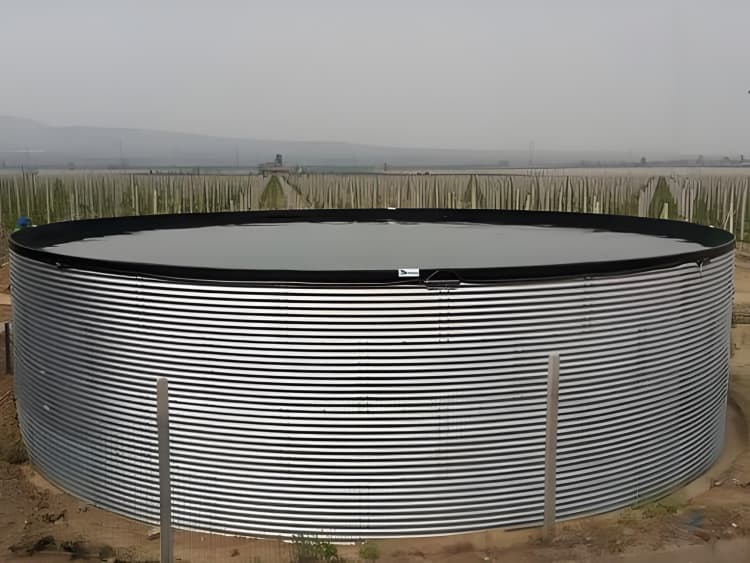
3. Long-Term Corrosion Resistance
- Triple-Protection Systems:
- Hot-dip galvanized base (150g/m² zinc coating)
- Optional 3LPE/epoxy linings for chemical storage (NACE MR0175 compliant)
- 30-Year Design Life: Verified in aggressive environments (mining, coastal sites)
4. Engineering Flexibility
- Custom Configurations:
- Diameter: 3m to 30m (AWWA D103-09)
- Capacity: 50m³ to 15,000m³
- Roof Options: Aluminum dome/steel cone/floating covers (API 650 Appendix J)
5. Zero-Maintenance Operation
- Leak-Proof Joints: EPDM gaskets tested at 1.5x MAWP (-0.5 to +0.3 bar)
- Inspection Efficiency: External-only 5-year checks (vs. internal inspections for concrete tanks)
6. Sustainable Performance
- 100% Recyclable Materials: Carbon footprint reduction vs. concrete alternatives
- Relocation Capability: Bolt disassembly/reassembly without structural compromise
Custom Configurations
- Diameters: 3m to 30m (AWWA D103-09)
- Capacities: 50m³ to 15,000m³
- Roof options: Aluminum dome/steel cone/floating covers
Technical Parameters (ASTM/EN Standards)
ParameterSpecificationMaterial Thickness1.2-4.0mm (hot-dip galvanized)Design Pressure-0.5 to +0.3 bar (EN 1993-4-2)Seismic PerformanceZone 4 (IBC 2018)Coating Systems3-layer polyethylene (3LPE) or epoxy
Project References
- 12,000m³ firewater storage for petrochemical plant (Qatar)
- 8-unit 5,000m³ grain ethanol tanks (Brazil)
- 30-year service life verification at Australian mining sites
Engineering FAQs
Q: Maintenance requirements?
A: 5-year external inspection cycle (NACE SP0169)
Q: Installation timeframe?
A: 30% faster than welded tanks (typical 8-week lead for 5,000m³)
Why Our Corrugated Steel Tanks?
- Finite Element Analysis (FEA) optimized designs
- Factory-applied cathodic protection systems
- 100% dimensional compliance with AWWA D103/EN 1993
- Dedicated BIM models for integration with plant designs
Note: “Bolted steel tanks” refers to the same product category throughout this document.